Hello all,
First, I would like to introduce myself, my name is Don Welch…I bet you'd never of guessed! My wife and I picked up a '67 Morris Cooper S earlier this year and I've been rebuilding it since. It was last registered in '83 and has been sitting ever since (as the story goes). Pulled the motor after a fresh rebuild because the diff bearing cages let go and never found the time to get it back on the road. Which is a good thing, as the car has been smashed in the rear, right rear quarter replaced (badly), along with several other issues that fall in line with his favorite saying "its what you did when you were 18".
Secondly, I would like to say thank you to many of you on the board, both those I've contacted for questions or parts, and those who've contributed to the posts I've been reading for the past 6+ months. Lurking and learning, edumicating myself on these cars that I've loved my whole life.
This car has been a big project, and some major headaches. But this is what I wanted, to learn something new and put my skills to use. I'm a first class metal machinist by trade, (lathe, mill, CNC programming, CAD drawing), welding (TIG and oxy acetylene), to fabrication of racing parts including oil tanks, brake adapters, drivetrain parts, roll cages, etc. Automotive wise, I have just over 10 years experience working on air cooled Porsches, mainly 911's and 914's. Rebuilding engines and transmissions, suspensions and auto body repair (panel repair, replacing, and painting).
Back to the mini, first thing was cleaning, inspecting, research, and rebuilding all parts. One of the hard lines needed to be patched, so I silver soldered a piece over the corroded area, then silver zinc plated both lines. The bags were cleaned out with methylated spirits to attempt to get all water and rust grime out, then blasted and painted. Each bag was pressure tested to 350psi nitrogen for 24 hours.
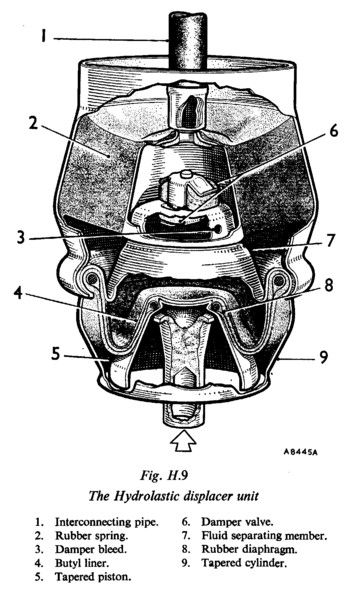
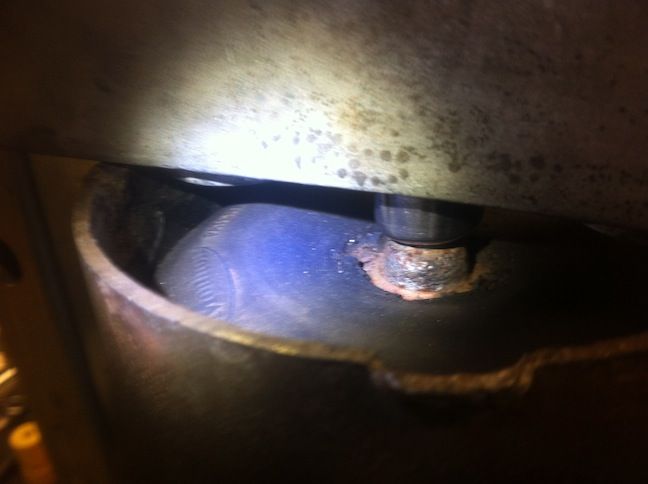
One of the bags' flexible line was damaged, so I set out to research what hose is available to replace this. I have not found anything as of yet that looks identical. The hose above is scrap from the bag I cut apart. The main problem is the crimped ferrule below the bag mounting rim… So I set out to solve this.
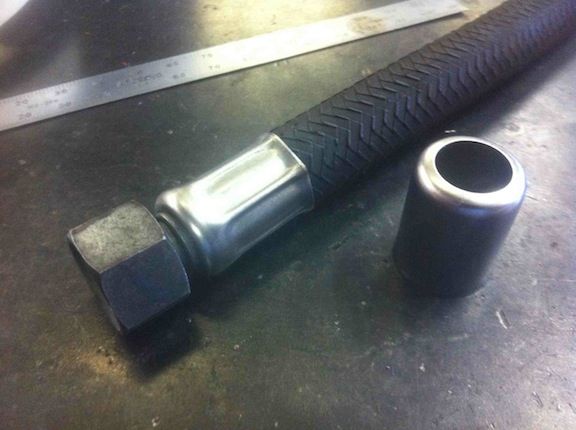
This is the same as the above picture with bag under nitrogen pressure. The crimp looks different (not flared at the top) because its wrong as I was working on the depth settings for the tool I made. It has been re-done (stupidly I did not get a photo of it), and it has been holding 250psi fluid pressure in my car for two weeks now. True test is yet to come...
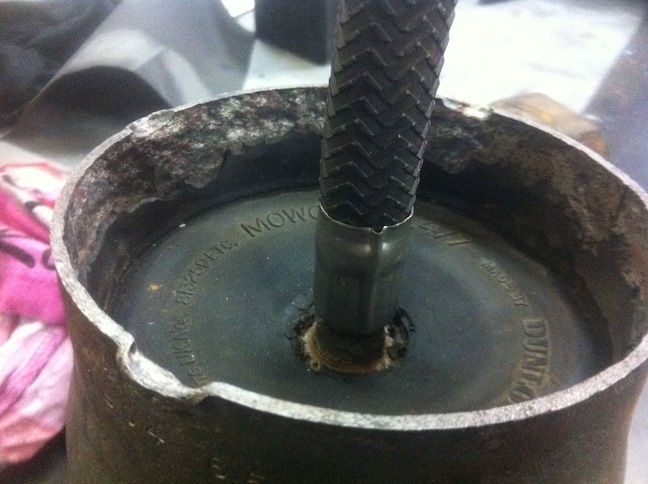
Another bag, which was a rear bag, had badly rusted around the bladder skirt (known as a Tapered cylinder #9 in the above cut away drawing). I was told this was black rust and should not risk using this bag. This was my chance to confirm the drawing, possible reverse engineer as well as do a few tests along the way. Using a spring rate tester, the inner vulcanized rubber spring is about 5000lb/in. I'm toying with the idea of making my own hydrolastic bags out of aluminium, interchangeable rubber springs for different rates, and serviceable for re-valving the internal hydro workings. I don't imagine there is much of a market, as most of the cars still running hydrolastic are doing so because they are collectables that came that way.
Cut away, yellow showing inner steel bell vulcanized to rubber spring.
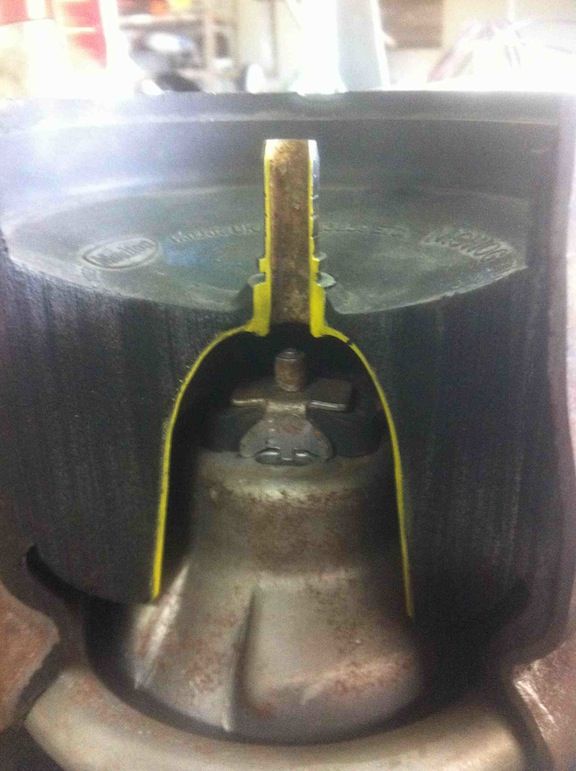
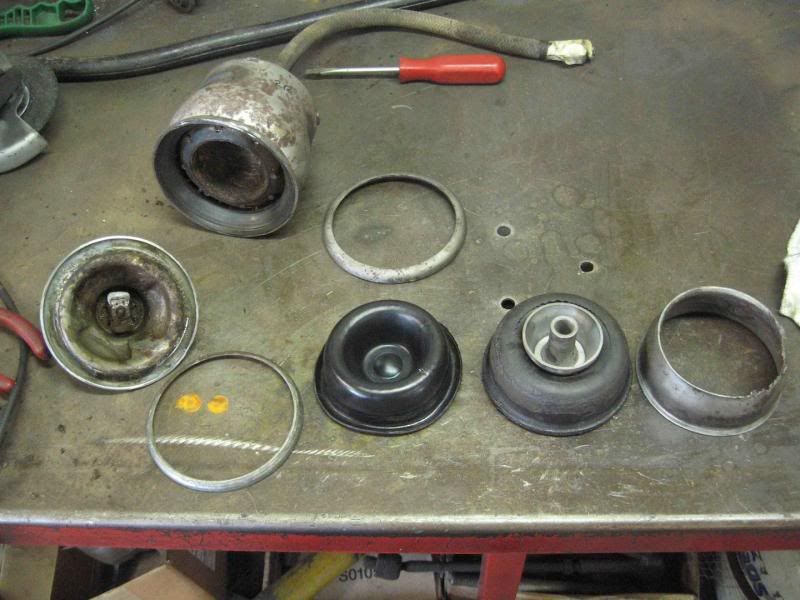
I'm also working on a tool that will allow me to open up these bags, so the internals can be properly cleaned, inspected, and or repaired. Then re-crimped so it looks like I was never there. Wishful thinking at this time, but time will tell.
I've made a hydrolastic pump that can pressurize at least 400psi and pull 20+" Hg vacuum, along with a jig to hold the hydrolastic bags and test them at pressure. I'm also making an electric motor driven cam/roller system that will bump the bag under pressure to depict road driving. These can be tested, even though there realistically cannot be a guarantee associated, there can at least be some reassurance that they will hold a standardized test. Especially considering how much of a pain these are to get in and out of the car.
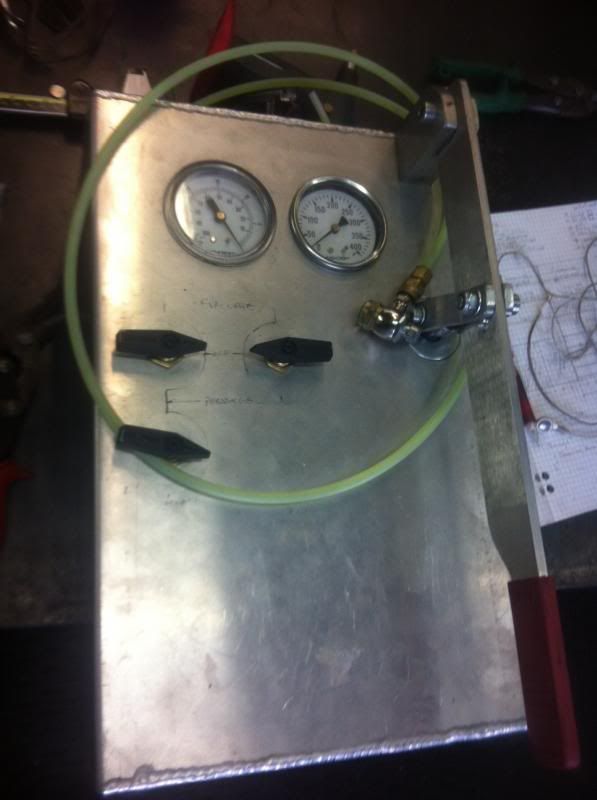
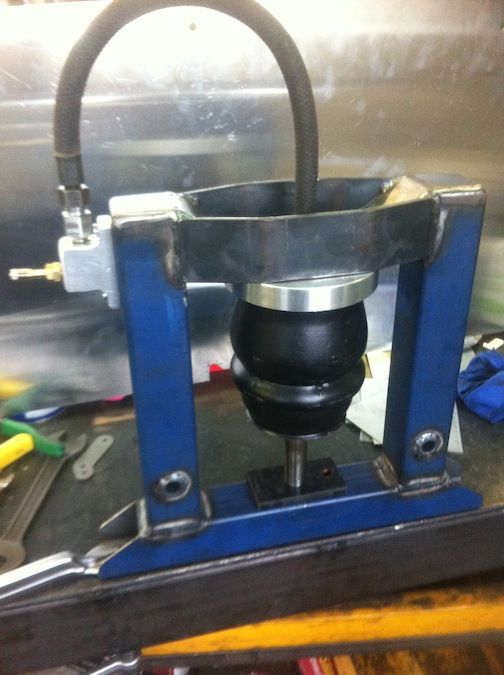
Now that this suspension and parts are reaching rare/unobtainium status, I encourage anyone who owns a business or has personal spare hydrolastic bags, please pull them out, flush them with methylated spirits, fill them with cheap coolant or another corrosion preventative fluid, and cap them. The saying "Worked when removed from car" is no longer comforting. I recently purchased a second hand bag, pressure tested it with nitrogen to 350psi and all was good. As soon as I put it in the car and pumped to 250psi fluid, within 3 minutes it ruptured through the rubber section. This can only be the result of the internal steel bell (yellow outline in the above cut-away) has rusted enough to break. Once you drain these bags, oxygen can enter and is the main contributor to oxidation… ie: rust. Even if you cannot be bothered to clean them, fill them and seal them. I will try to come up with several cheap ideas of sealing these, or even make some cheap caps it there is enough interest.
Rupture
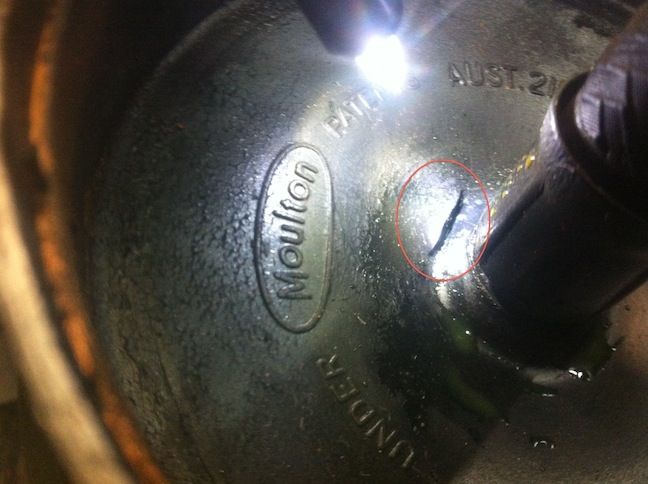
Thank you for you time, Don.