Hi Guys, thanks heaps for the kind words and the support for the project, means a lot...
Anyway, I thought I would update this thread again, as the build is actually a fair way ahead of where the thread is, and I need to be a bit more diligent about keeping this updated - sorry Justin!!
And speaking about Justin, can I just say what a top bloke he is - not for paying the invoices on time, but for his unwavering focus for the project. This project is fairly lengthy (well, not if you compare it to The Cat, but that is another story!!) - and a lot of people would have diluted the project down just to reduce the time or save some dollars - not Justin - his steadfast commitment to the original design intent - that of a race-ready/fast road car is worthy of mention. His vision for the car in his minds eye is resolute and unbending - that folks takes cohones. Justin also asks a lot if questions and even challenges me on occasions if he thinks that an area of design is not in the best interests of the project or could be improved - this shows that he wants to be involved, have input and share the outcomes (good or bad!!). For instance, Justin has brokered a deal with Skunk2 in the USA to supply some engine parts for the F20B - he did this on his own volition without any prompting from me as a way to improve the end result. We thank Skunk2 for being a part of Leonidas, and I also personally thank Justin for having the stones to approach Skunk2 in the first place - well done mate!!
Anyway, enough about Justin and more about me, err, Leonidas.....
Last time we met we had finished the lower subframe mounting points and binned the original bootlid in favour of a lightweight fibreglass item because it was too uneconomical to repair. Moving on with the structural side of things, the last element of the sutructural support is ready to be done - the front upper mounts. This structure has to do some other tasks as well - it needs to provide mounting points for the subframe as previously said, provide support for the 12mm Lexan window, provide a mounting point for the firewall and provide hardpoints for the racing harness mounts. While this sounds like a lot of multi-tasking, the structure is actually very simple- its basically a transverse piece of RHS welded in place. The location for the bar was also set in place - basically to the rearmost edge of the upright bulkheads. This will allow the firewall to slope backards slightly, and provide some space behind the seats for the rollcage install, mounting the ECU and other bits to the firewall between the seats and also a small bit of storage behind the seats for things like helmet bag and the occasional dead body (wtf I hear you say, you will never get a dead body behind those seats - and you are right, wont fit - delete the part about the dead body damnit

)....
A piece of 40x40x2.5mm RHS was chosen for the task. This will allow a flat surface for the 12mm Lexan to sit on, and also a flat face for the firewall to butt up to. It was cut to size and welded in place:
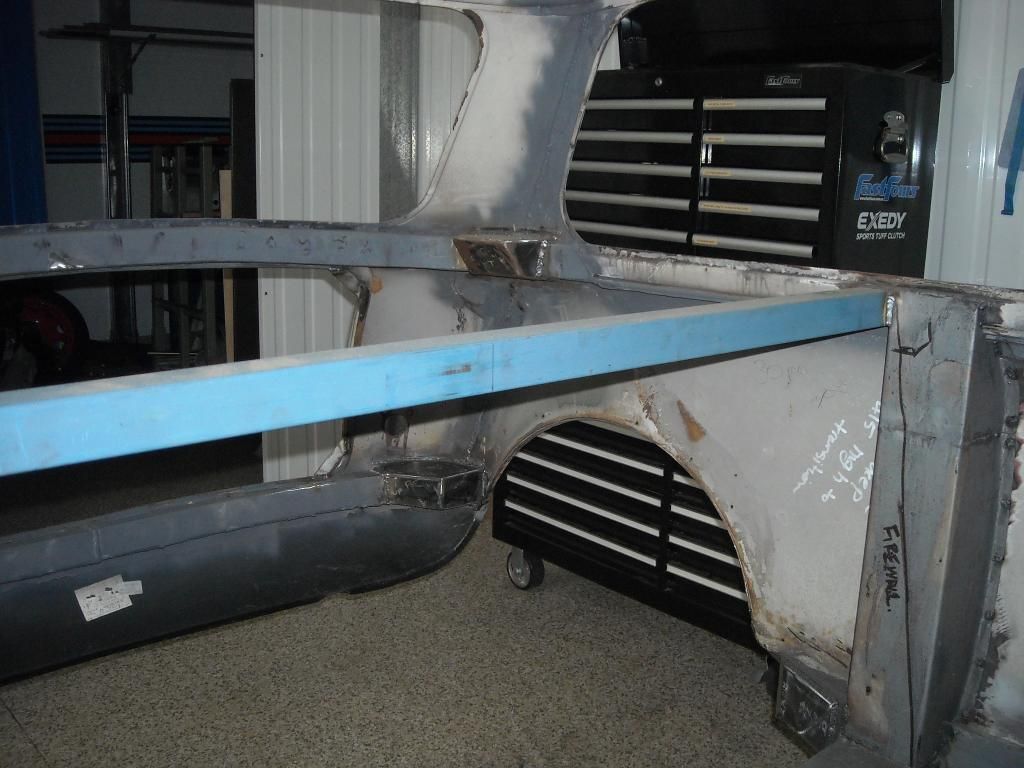
Note: What I havent shown is the mounting points for the subframe - 2mm plate with captive nuts welded onto the bar. My apologies for this as the camera took a dump!

These points will show up in later photos of the subframe itself mounted up....
With the bar in place I could check seat fitment. Justin had chosen a nice set of Sparco 333's for Leonidas. They were a really good choice - lightweight, comfortable and very supportive and they also came with the apertures for the harness shoulder straps built-in. I made up some seat bases for the seats from 40x3mm strap - it ididnt need to be anything too heavy, but substantial enough to cater for the loads imposed. The back part was bent into a U-shape, while the front was designed to butt up to the original Mini transverse crossmember as the front support element (as per original Mini). The front of the seat rails is mounted directly on top of the crossmember, so this aread has to be reinforced. I used some 2mm plate, with captive nuts wleded to the underside, and then welded those to the crossmember at the four bolt locations - a bit overkill but there is zero chance of shear now:
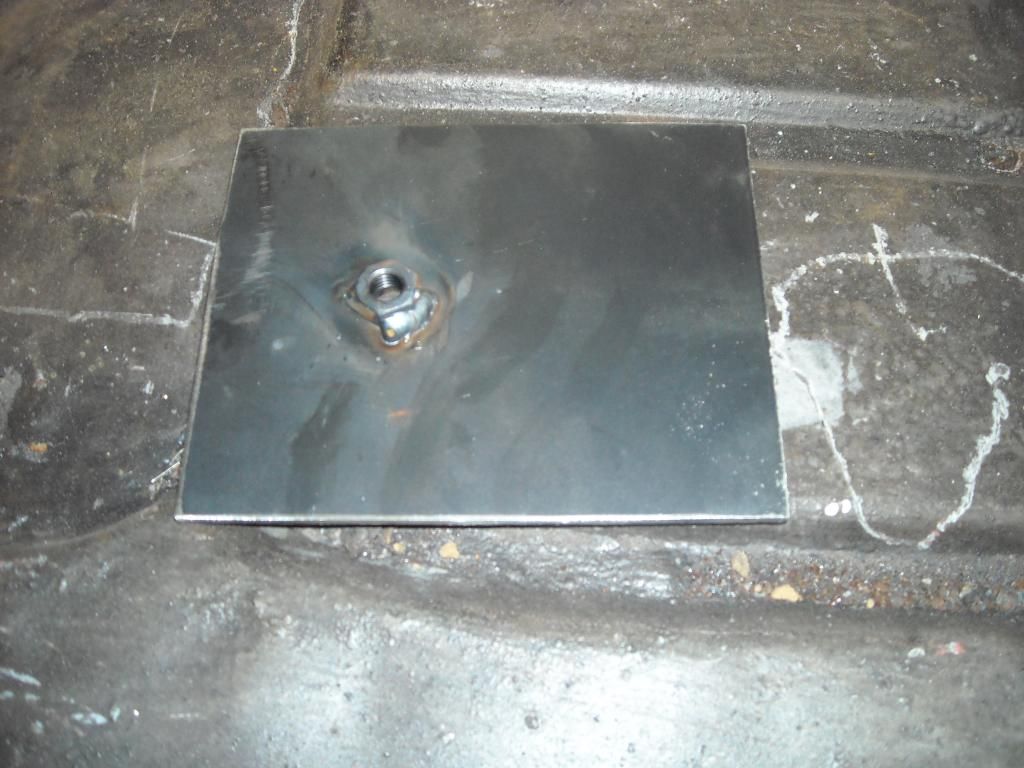
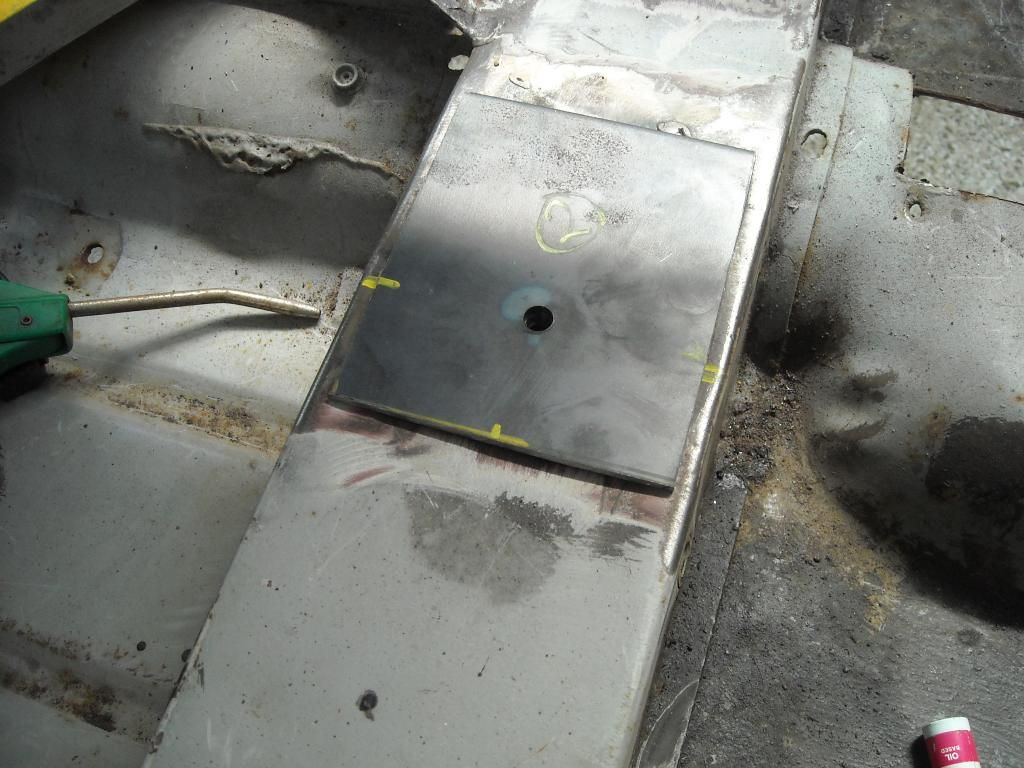
3 x M8 grade 8.8 bolts hold the front part of the seat base to the crossmember using nutserts into the crossmember, while at the part 2xM8's go through the reinforced floor to anchor the rear of the seat base:
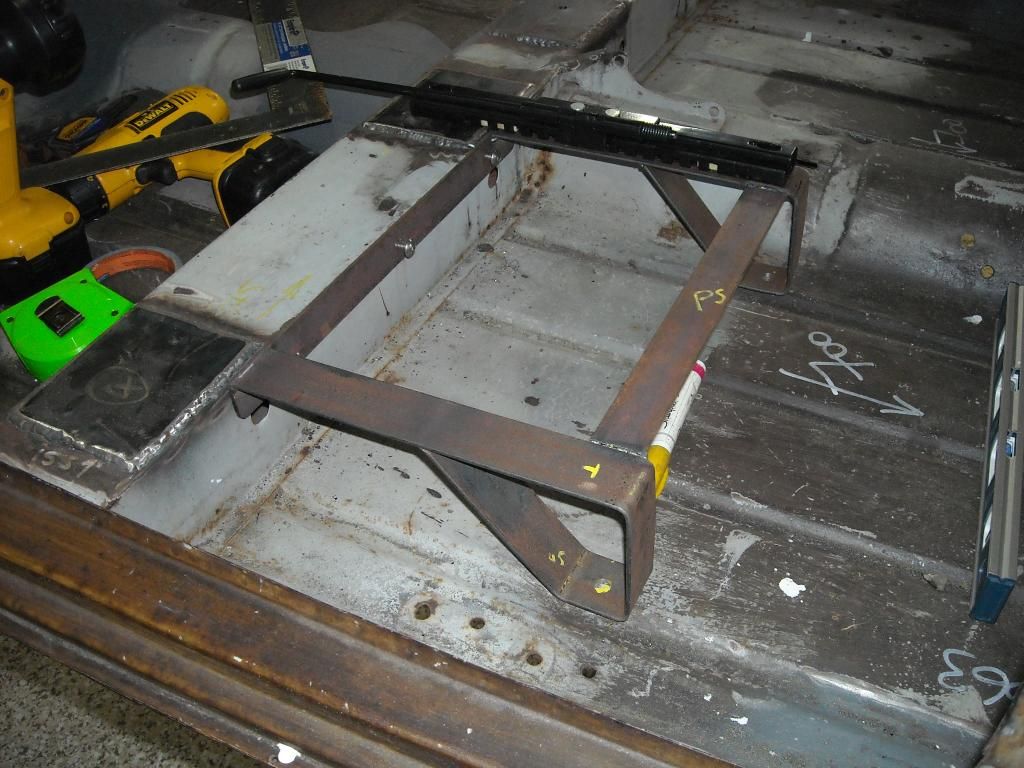
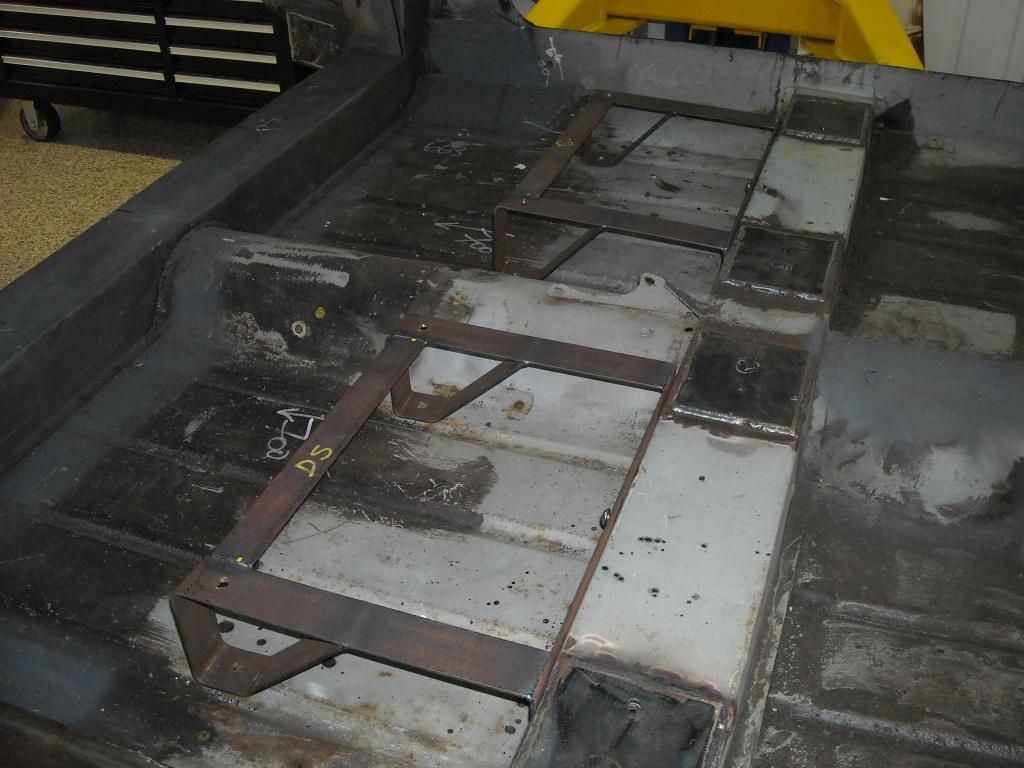
Mounting the seats I tested their extent of travel along the seat rails. While the limit of travel of the rails was achieved in both directions, the angle of seat recline was limited by the rollcage/firewall location. Testing showed that we could get three clicks of recline from the vertical position, which should be enough for most drivers I would think.
Seats in position - Sparco 333's, a really nice seat:
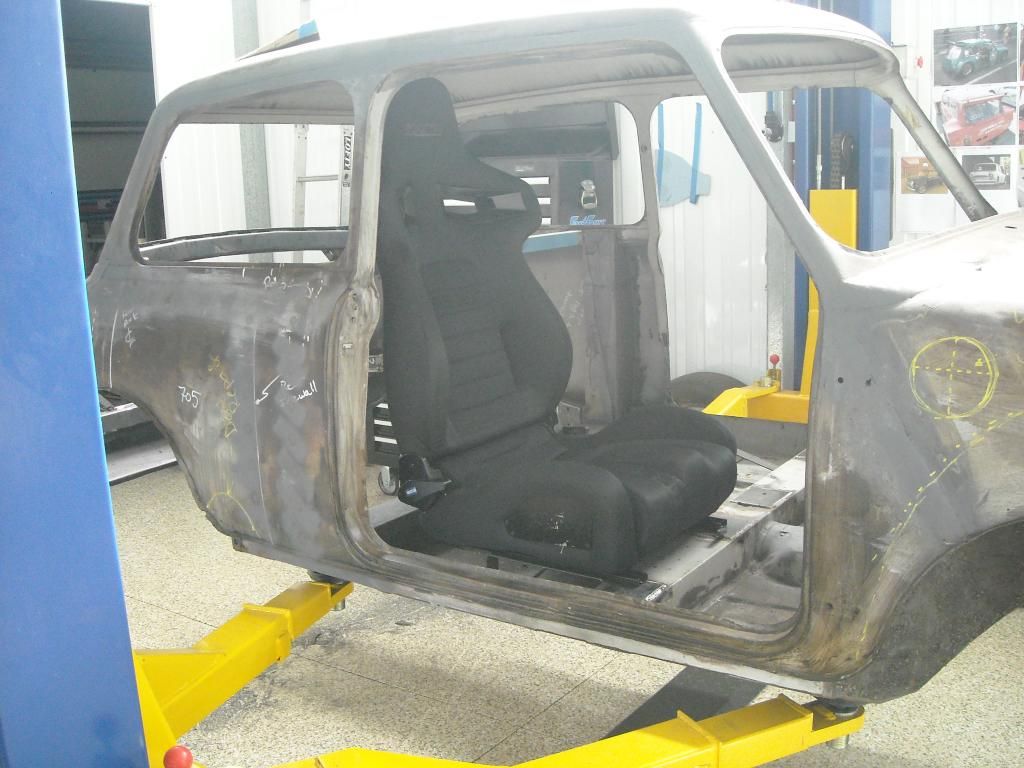
Enough room???
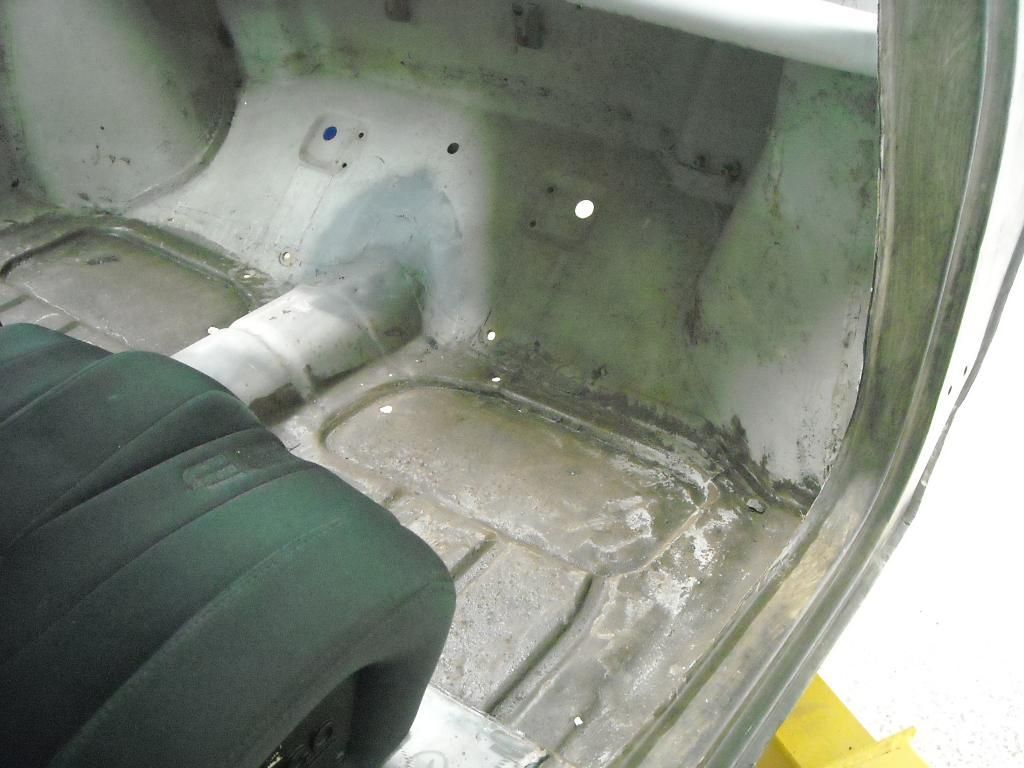
Me, in the seat - I'm 5'8", Justin is a little taller, but my legs are straight and I can just touch the firewall even with boots on:
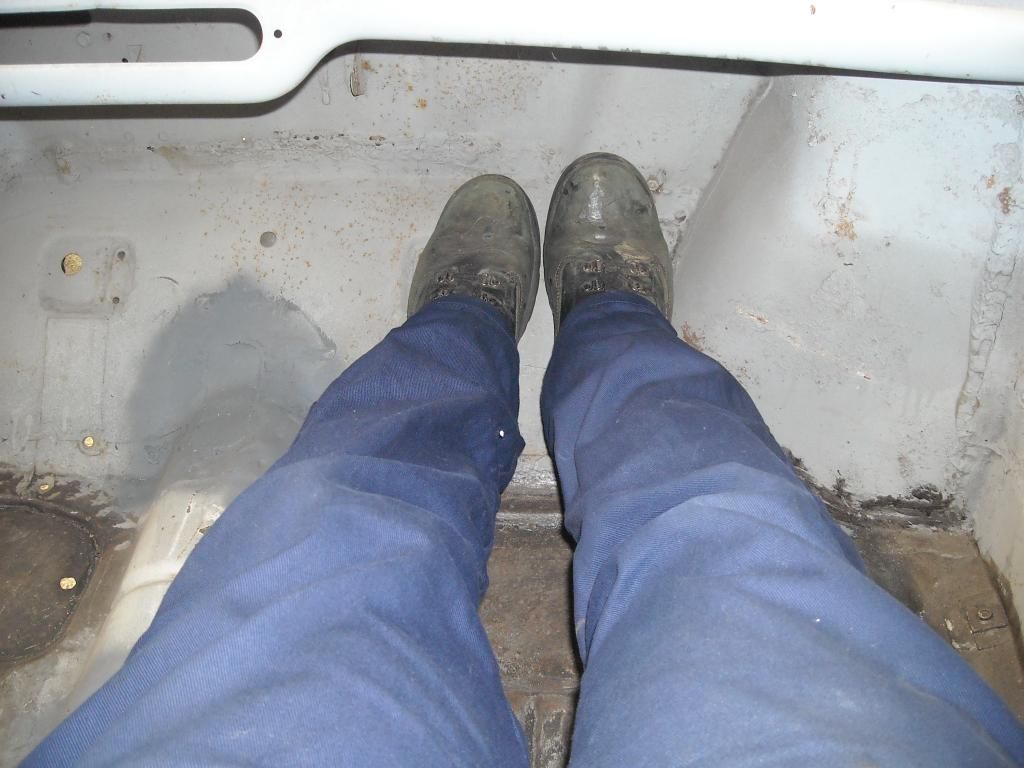
Seat back travel - upright position with the seat in its rearmost position on the seat rails:
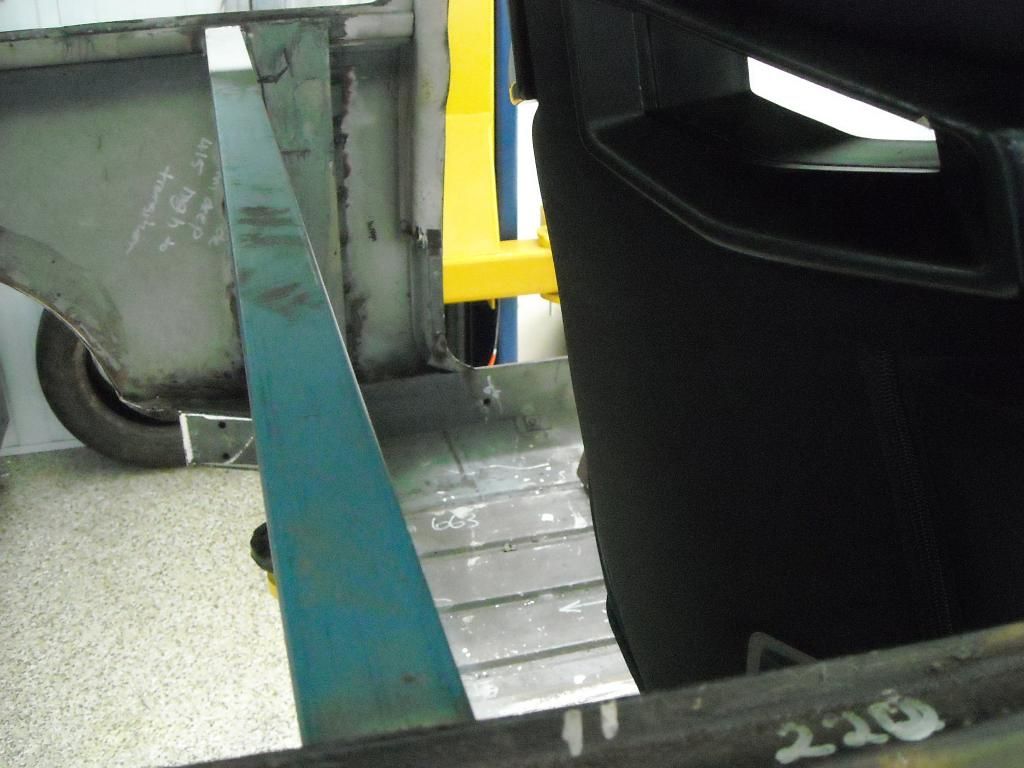
2nd position - preferred by me as I like an upright position:
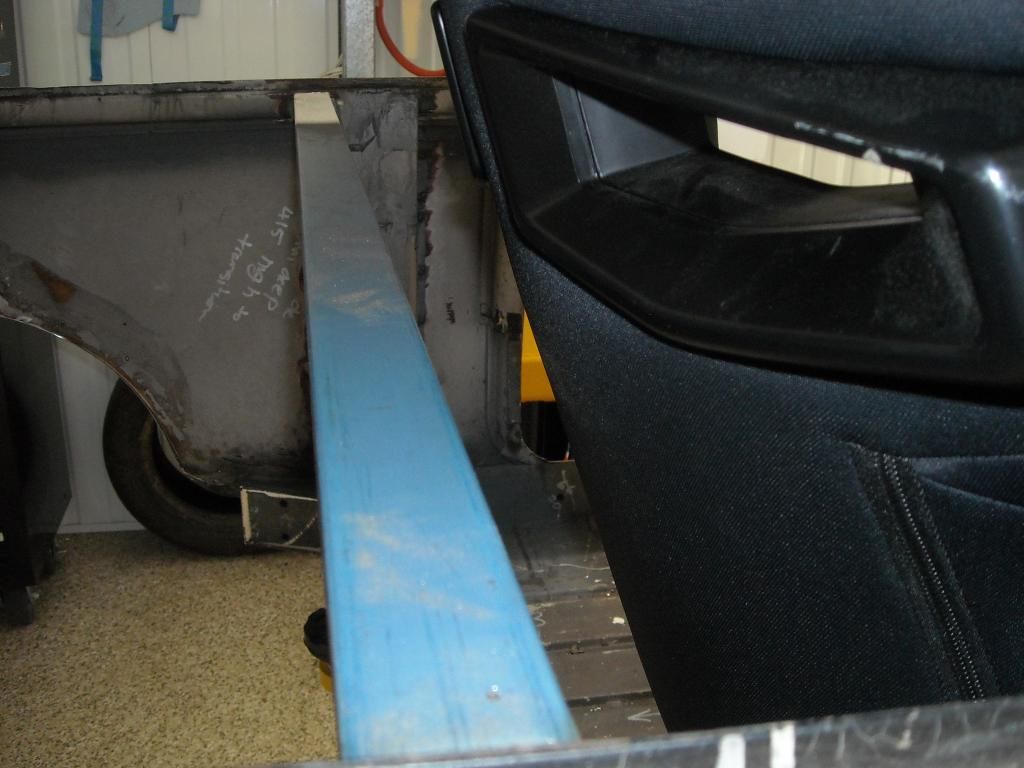
3rd position with the seat at its rearmost travel - the rollcage diagonal brace may interfere slightly here:
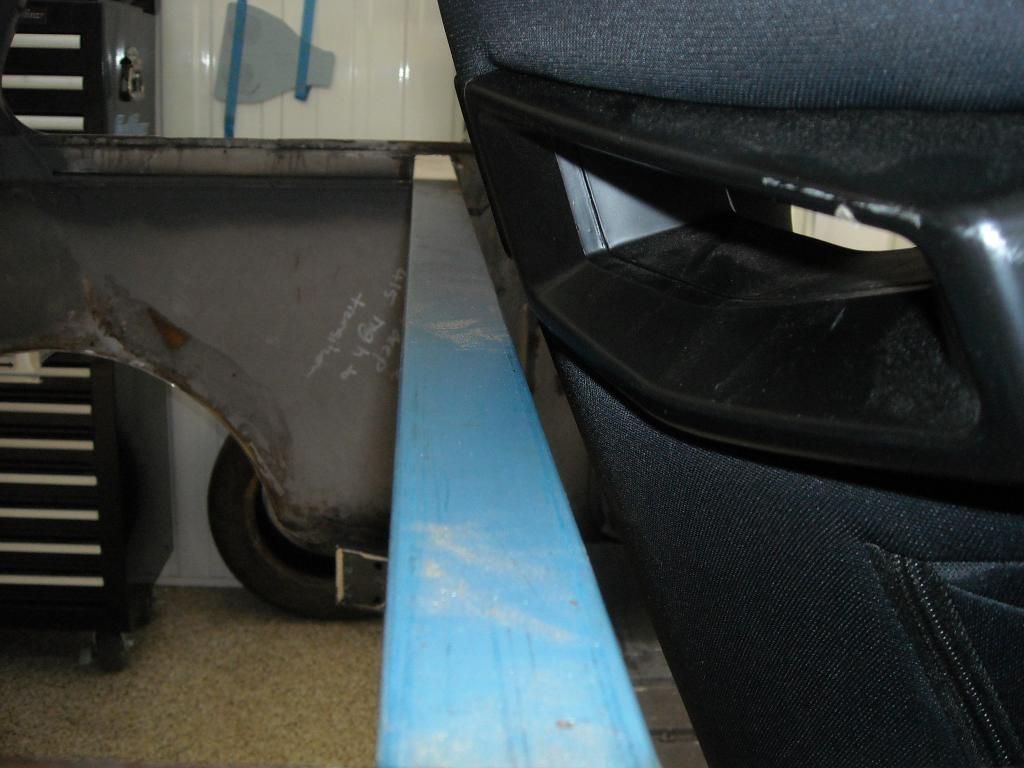
Seats done - check! Next I decided to take a detour from doing the structural stuff (albeit almost completed now) and move onto doing something a bit more creative (the whole project is 'creative' - what you talkin' about Willis??). I decided to tackle the fuel filler location just for some razzle dazzle and send Justin some pics of something other than structure. Since the fuel tank is to be located in the front, a fill point had to be fabricated at some point. Justin wanted it external, and on the drivers side - good choice. I suggested a motorcyle-style filler, similar to El Gato - inset into the guard. I sent Justin some pics off the Interweb of what I was thinking and he said how visionary and creative I was and to go ahead!

So, off to the motorcycle wreckers and I grabbed this - a dented fuel tank from a late model CBR600 (in keeping with the Honda theme!!). I took it around to a mates Locksmith shop and got the lock picked and three keys cut, as it didnt come with any keys - total outlay was $85 for the day. Here it is with the filler cutout:
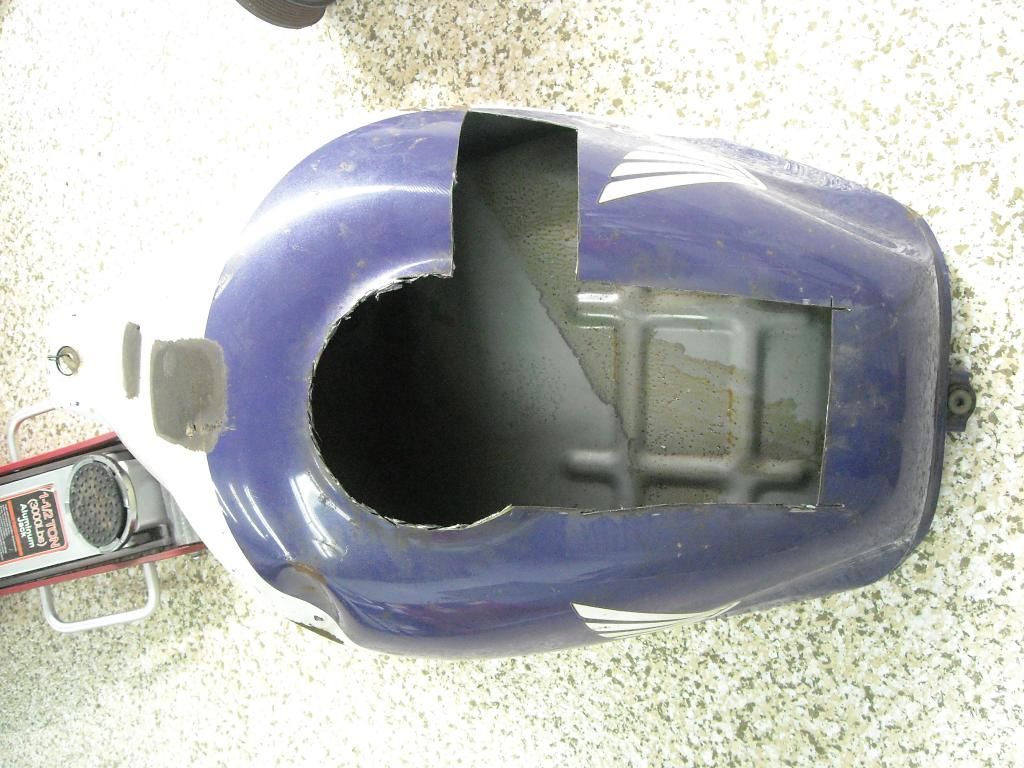
Said filler assembly:
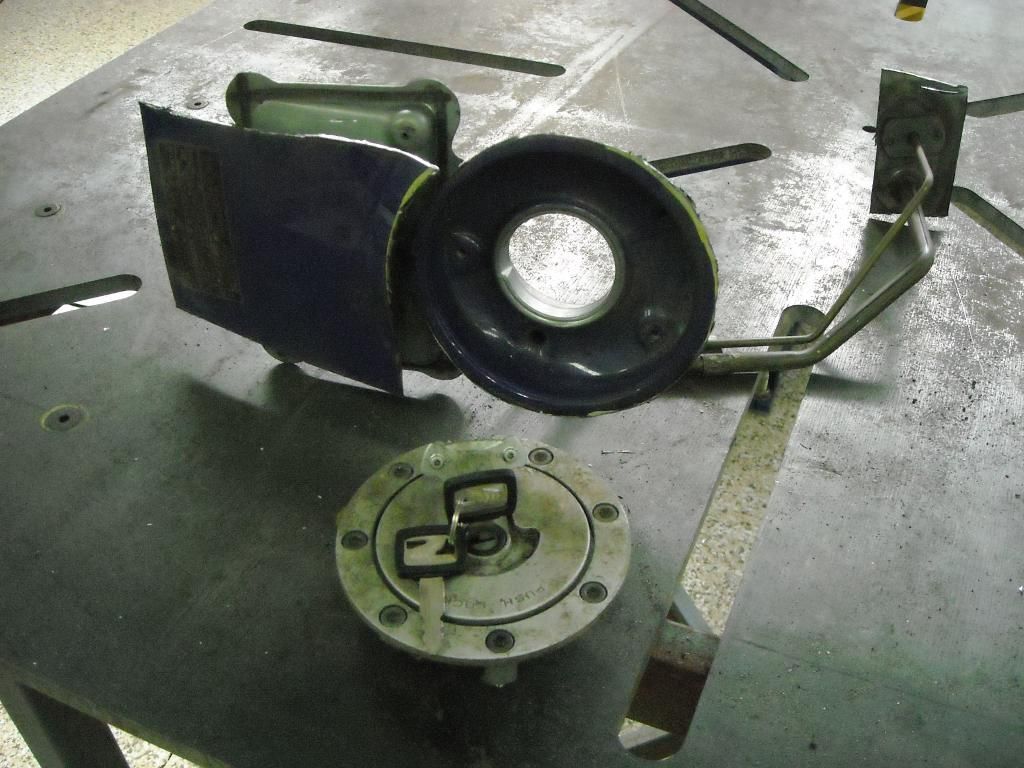
Trimmed to size and read to got in:
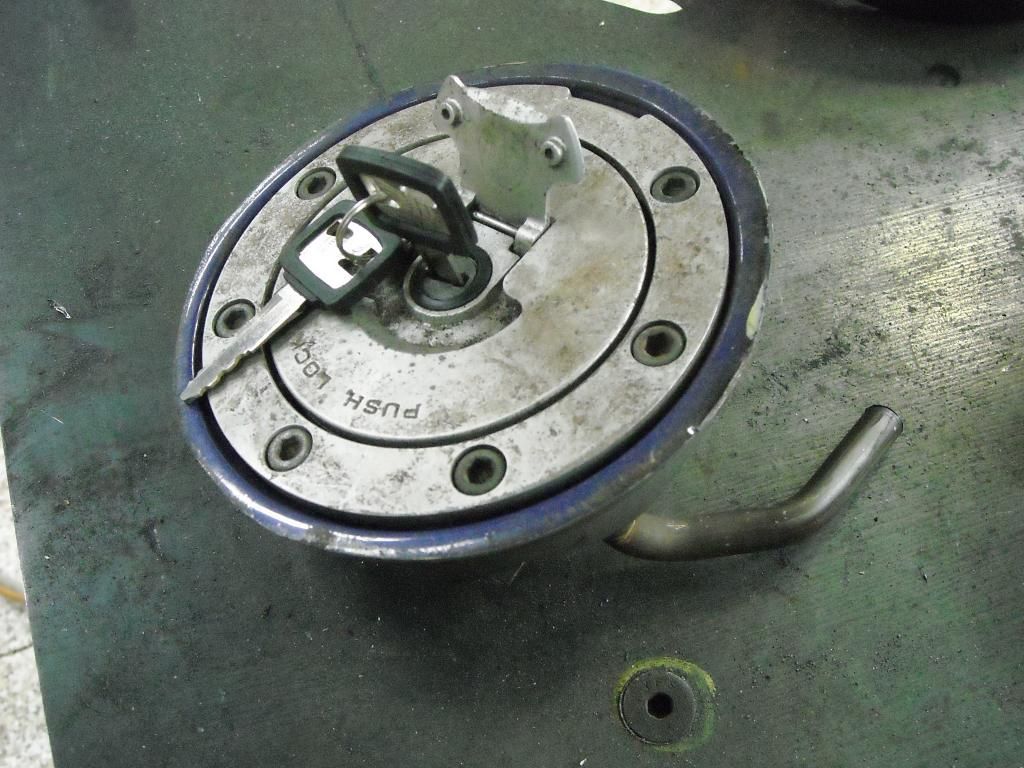
The final position of the filler was determined by the tank shape, guard profile, fill height of the tank, and the alignment of Venus in the house of Gemini:
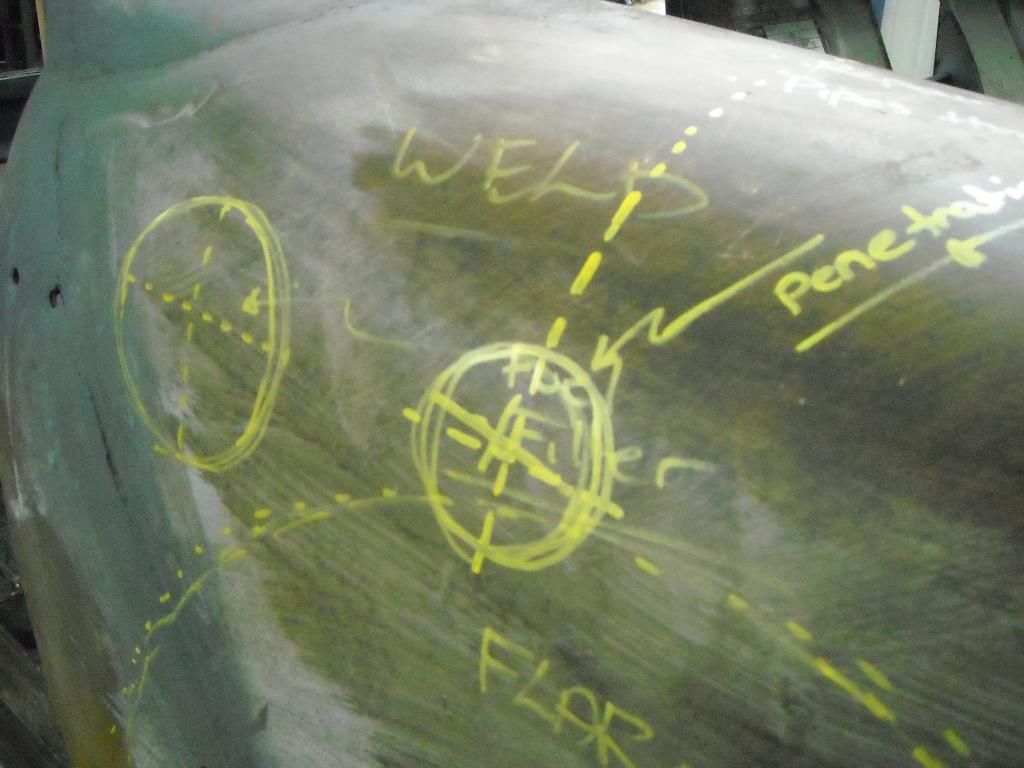
It couldnt be too high, as the guard profile was too rounded, and it couldnt be too low as it would not allow enough fall to fill the tank safely. It also had to align up with the area I had chosen inside the (old) engine bay for the entry point. Ahh yes, just right (top hole as 'X' marks the spot:
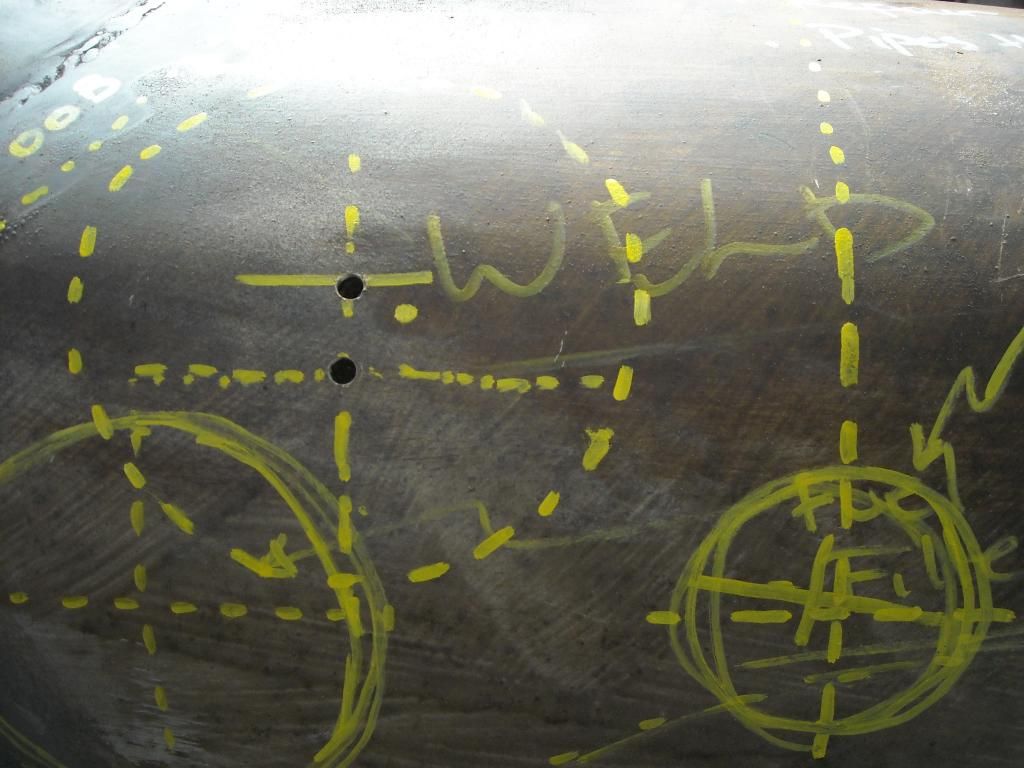
Then out with a whopping big holesaw and cut the guard out (what have I done, no going back now!!):
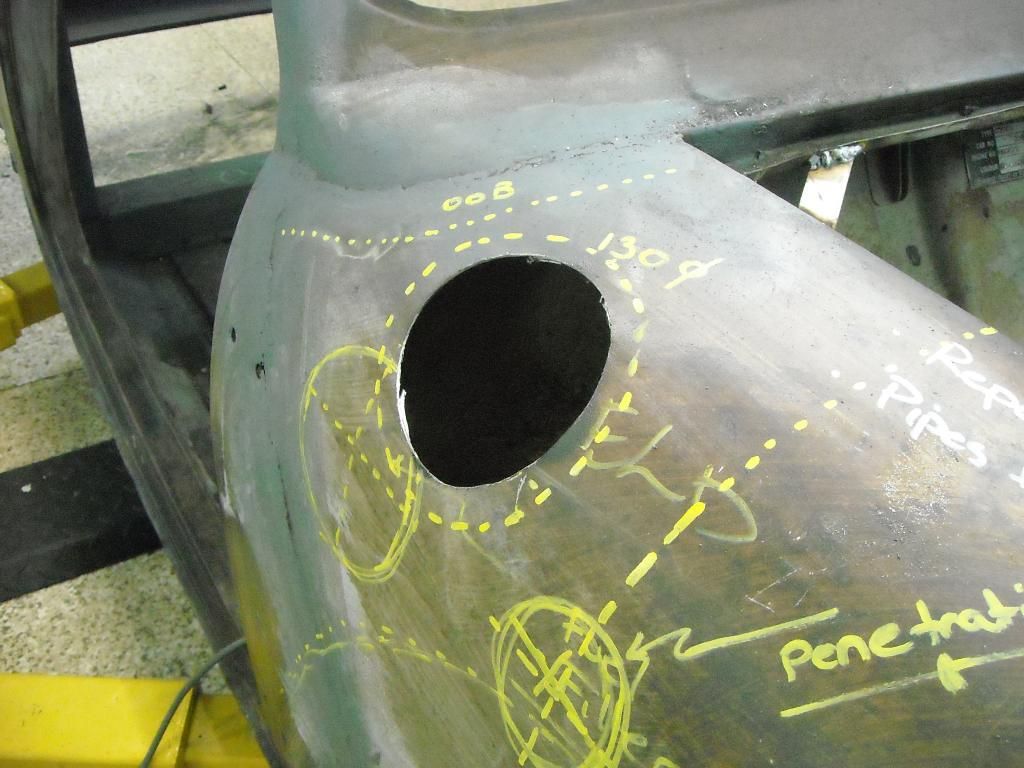
Then, make up the surround to fit around the filler neck - a kind of collar if you like:
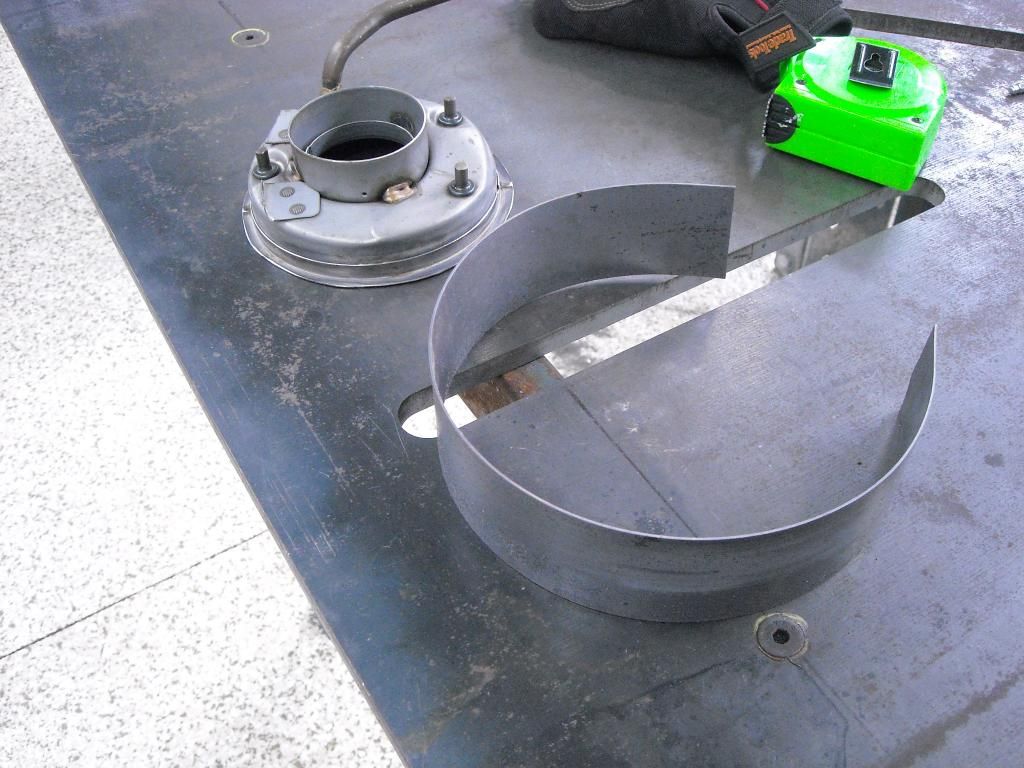
Weld it on and clean it up. Filler neck also done:
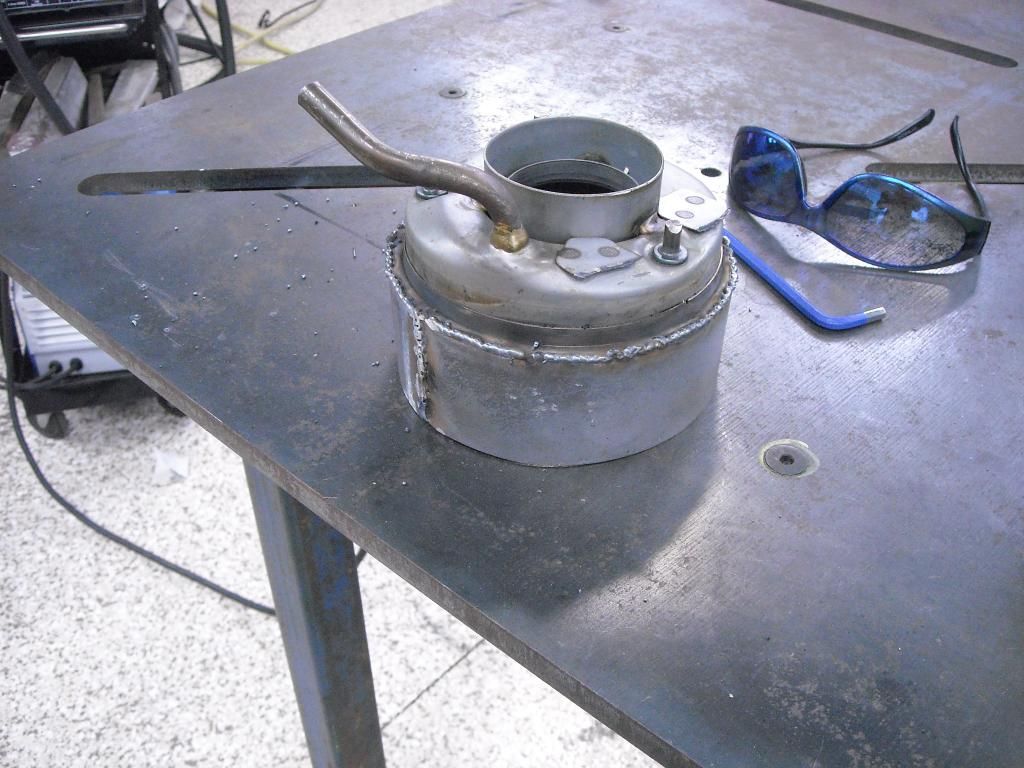
And then insert it into the big whopping hole, hoping it all is roughly the same size (of course it is, its engineered after all!):
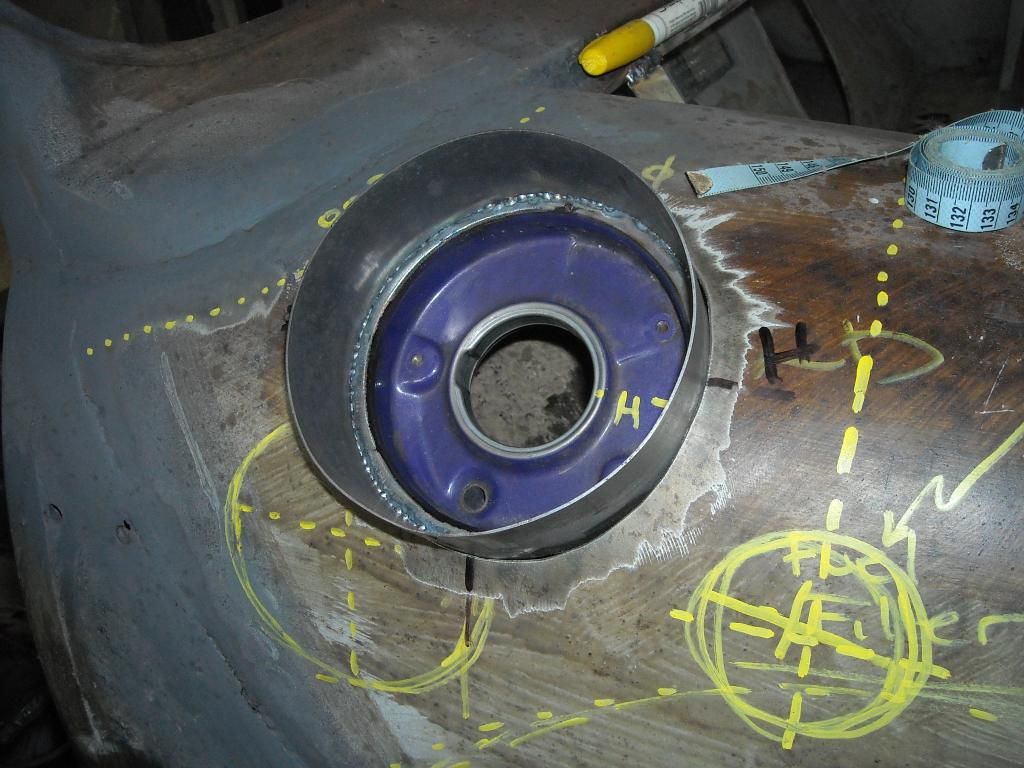
Happy with the fit and position, tack it in place. Make sure the filler 'lid' swings the right way:
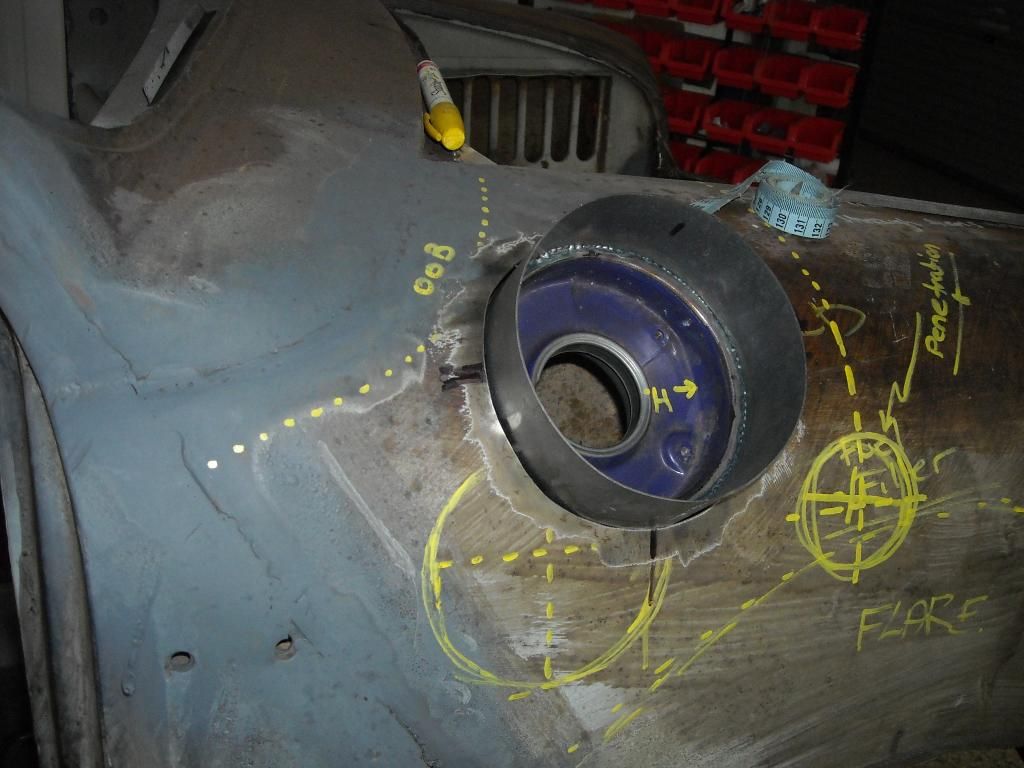
Weld it in from underneath where you can, and from the top where you cant:
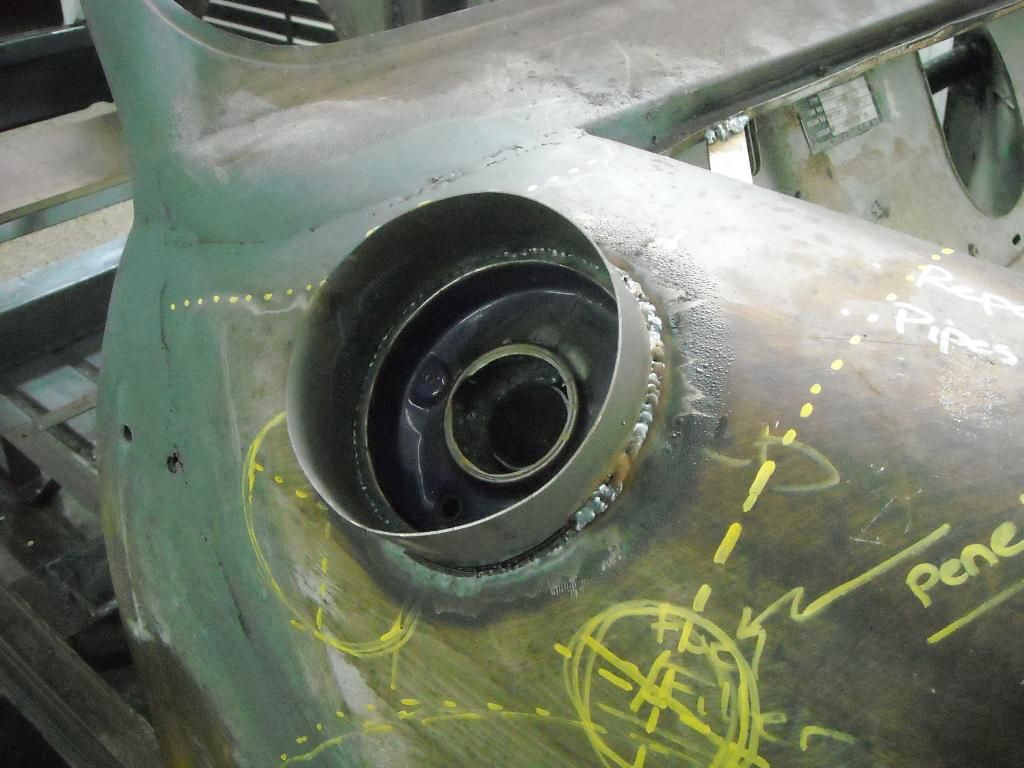
Cut away the excess collar, and clean up with the flap disc. How's that for razzle dazzle??? Notice the lid swings to the front - this is so that if Justin forgets to lcok it securely, the onrushing air stream will hold the lid down and not flick it open:
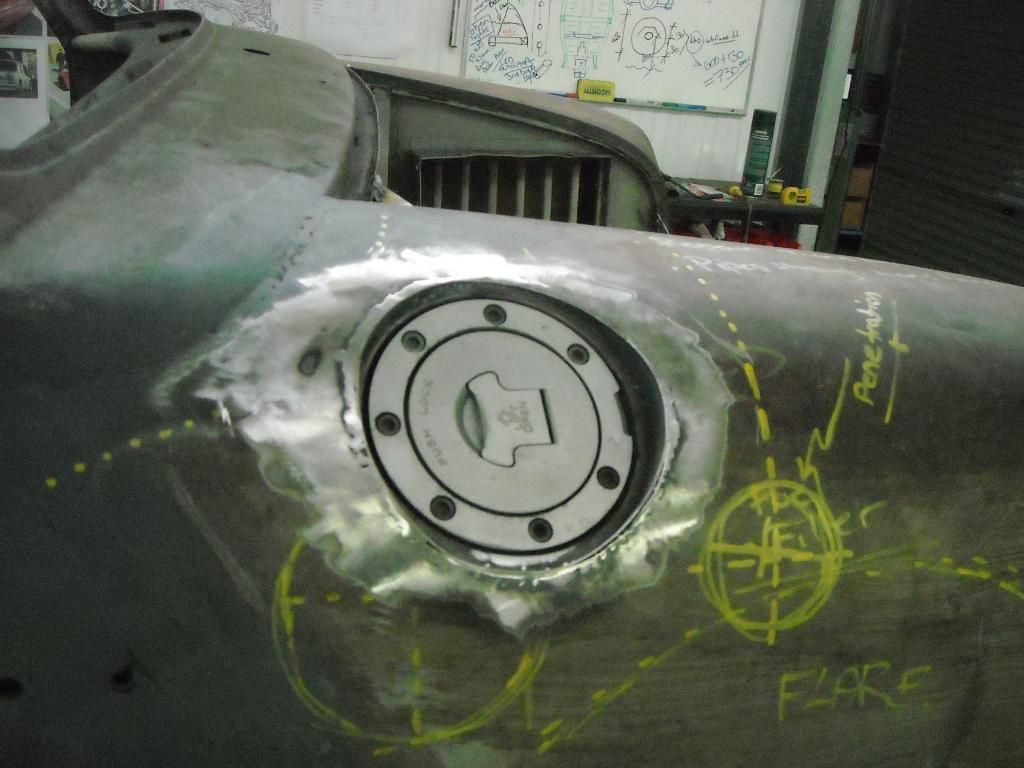
Prior to welding in, I welded on an elbow to the underside fill neck to allow the flow to turn 90-degress. Then it would turn another 90-degrees into the (old) engine bay. Here is the 90-degree bend underneath the guard. You can see the entry point into the engine bay:
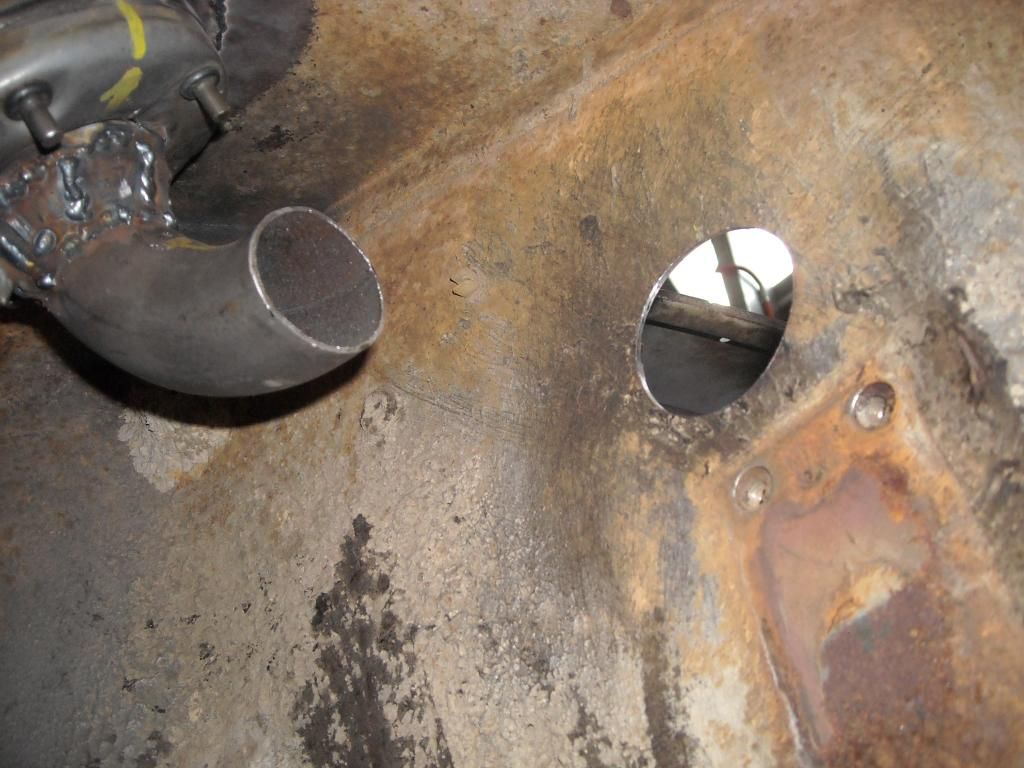
And, perfect alignment with where I wanted the fill-pipe to come in. From here it will do another 90-degree bend into the tank. It should fill just fine, albeit a little slow:
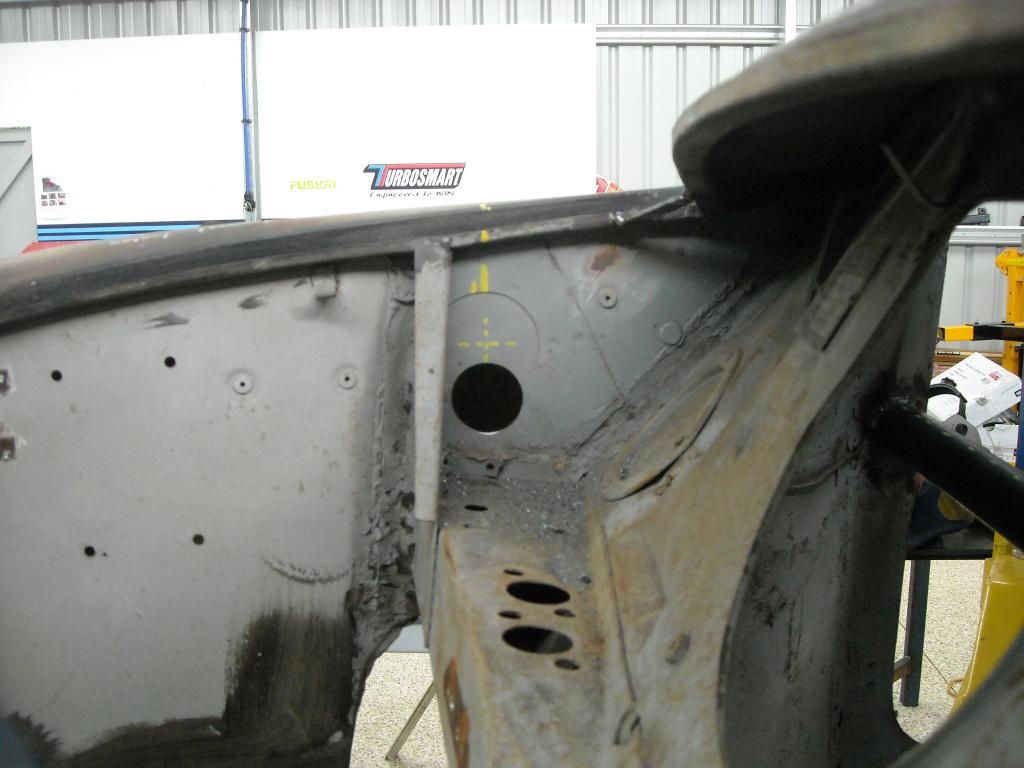
More soon.
Cheers,
Tricky