There are many versions of the Eaton M45. There are the ones that were fitted by OEMs like the BINI one and the ones fitted to various Mercedes cars. There are also generic ones you can buy that don't have the extras like the big snout inlet or the water pump drive that the BINI one has. Without those in the way the inlet is straight into the back.
Here is a pic of a generic one that was part of a Jackson Racing SC kit I had on my MX5.
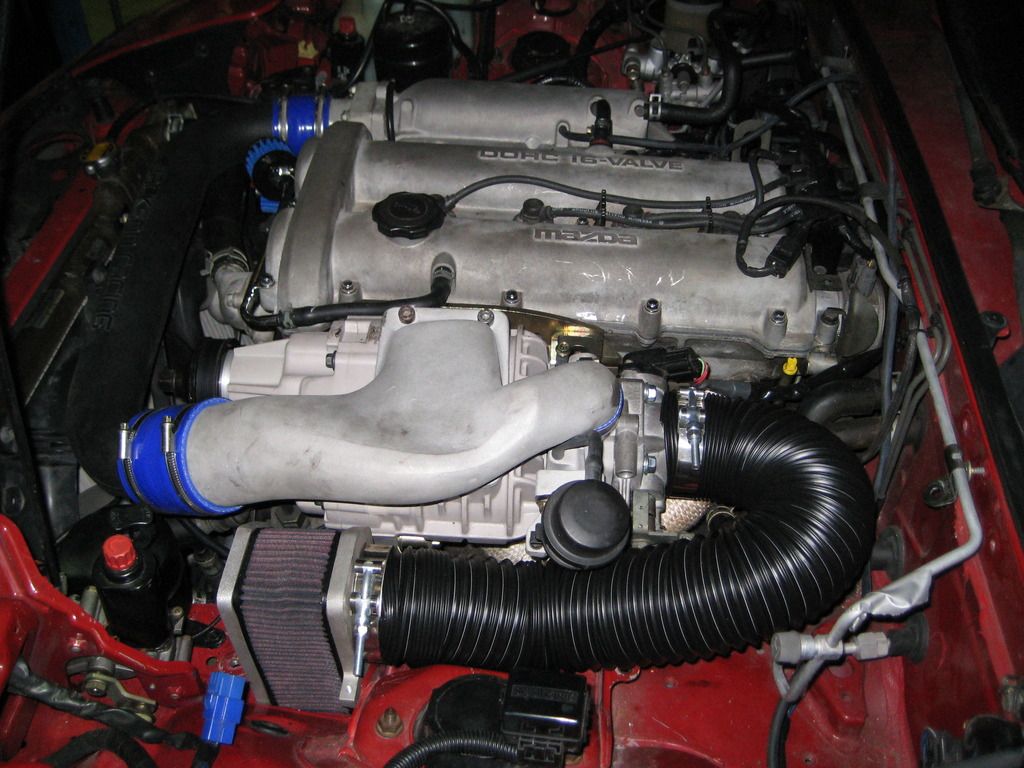
This one has a cast outlet manifold to suit the MX5. It has an adaptor so the MX5 throttle body bolts straight up to it and it can use the bypass valve for idle.
There has to be a reason why all car manufacturers who fit M45 chargers use an idle bypass valve. My guess is that at low revs and with a high vacuum at idle the charge pulses make for a crappy idle. The bypass valve is vacuum opened spring closed so it closes as soon as you hit the throttle. None of the M45 kits for a mini appear to use the bypass valve. Maybe that is contributing to the issue?
There are some fundamental rules for gases:
a) Compress a gas and its temperature goes up,
b) Expand a gas and its temperature goes down,
c) Compress a gas 'inefficiently' (by stirring it around or pumping it around corners, through small holes etc) and the temperature goes up more that it otherwise would.
d) The amount of water vapour that can be stored in a volume of air is limited. Above a certain value and the water vapour condenses out as liquid water. This limit changes with temperature. Cooler air can hold less water vapour. Hence dew forming on a cool night, water coming from an air conditioner and dams evaporating on hot days. This is why the BOM give humidity as a %. 100% is when the air can't hold any more water vapour. Your sweat won't evaporate and you can't cool down.
e) When liquids change into gasses, they absorb energy in the form of heat. This is the principle behind evaporative coolers and how people cool down by sweating.
The Vmax kit does some of everything above. When the throttle is closed, the air between the throttle and the engine is in a partial vacuum. It passes the throttle and expands, getting cooler. Cooling is exacerbated by vaporisation of the fuel which starts as a liquid and turns into a gas, absorbing heat as it does so and reducing the temperature. There is hardly any fuel being used at idle so this is not the major cooling contribution but it is still important. When the air cools it will likely cross the limit of water vapour capacity unless it is an extremely dry day. The water vapour (humidity) condenses out as liquid droplets. These stick to the side of the inlet pipe and form drops which run back down towards the throttle. At the throttle, where the cooling effect is most pronounced, the water can freeze and cause sticky throttle or change the amount of open area around the throttle disc.
When the Vmax kit is on open throttle, there is negligible cooling of the inlet as there is very little pressure drop through the air filter and carb. The air/fuel mix goes into the charger and gets stirred around and pushed through. This stirring a pumping through the innards of the charger in itself doesn't make any boost but it does heat the air up. The outlet side of the charger is pushing air into an intake with valves closed most of the time and when they are open they draw less air than the charger delivers. This means the air from the charger is being stuffed into an intake and this is why the pressure goes up. The air/fuel charge is sloshing around in there like a drunk on a bus as the charger lobes pulse incoming air, some leaks back around the ends, some goes towards an open valve and picks up momentum only to be stopped by the valve closing. All this generates more heat than the minimum that is generated by just the compression of the air. There is no intercooler to dump this heat so it goes into the cylinder, increasing the peak cylinder temperature, decreasing the density of the charge for a given pressure and therefore the amount of oxygen and fuel that can be burnt and bringing the whole lot closer to the pre-ignition temperature/pressure limit of the fuel used.
To improve the application of a supercharger to a mini while still keeping it fed by a carby you need to:
1) Minimise the air volume that is under vacuum at idle - Put a throttle disc near the charger inlet. It doesn't have to be the whole carby, just the throttle. You could keep the carby where Vmax put it but take the throttle out and block the shaft holes.
2) Make sure that the air does down hill between the throttle and the engine so any condensation goes in the engine and not back to the throttle disc where it can cause icing issues.
3) Improve the outlet geometry (charge to head manifold) to get as smooth a flow as possible and, if you can, get some intercooling in there. You won't want a blow-through air to air charger, it would be a bomb. Maybe a sandwich water to air like some Ford V8s have.
4) Consider fitting an idle bypass valve. As noted above, every factory set up has one so there must be some benefit.
5) If you have the cash, swap the charger out for the Magnussen one that Low'n'blown suggests. These are direct replacements for the (generic, not BINI) M45 and M62 Eatons. They (apparently) have some twist to the lobes and generate some compression within the device. That is they are a semi-screw charger and are more efficient. The Sprintex and Opcon Autorotor ones are even better but not direct replacement. The efficiency change is very large when going from a Rootes to a screw compressor so it is worth it but none get close to a well made turbo or centrifugal compressor.
M